
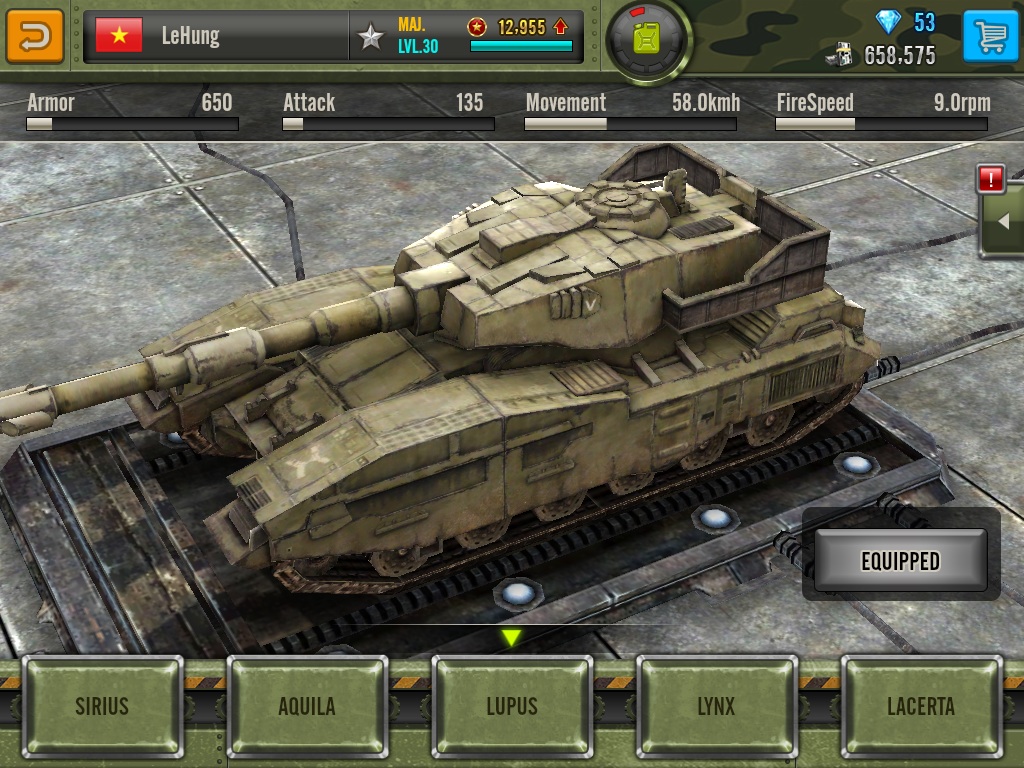
P is no longer much, much less than Pr/t and Pr/2t), and so the thickness of the wall becomes a major consideration for design (Harvey, 1974, pp. Σ θ = F t l \sigma _ is less than 10, the radial stress, in proportion to the other stresses, becomes non-negligible (i.e. The hoop stress is the force over area exerted circumferentially (perpendicular to the axis and the radius of the object) in both directions on every particle in the cylinder wall. Cylindrical vessels of this nature are generally constructed from concentric cylinders shrunk over (or expanded into) one another, i.e., built-up shrink-fit cylinders, but can also be performed to singular cylinders though autofrettage of thick cylinders. These compressive stresses at the inner surface reduce the overall hoop stress in pressurized cylinders. In thick-walled pressure vessels, construction techniques allowing for favorable initial stress patterns can be utilized. Thin sections often have negligibly small radial stress, but accurate models of thicker-walled cylindrical shells require such stresses to be considered. Similarly, if this pipe has flat end caps, any force applied to them by static pressure will induce a perpendicular axial stress on the same pipe wall. In a straight, closed pipe, any force applied to the cylindrical pipe wall by a pressure differential will ultimately give rise to hoop stresses. The classical example (and namesake) of hoop stress is the tension applied to the iron bands, or hoops, of a wooden barrel. These three principal stresses- hoop, longitudinal, and radial can be calculated analytically using a mutually perpendicular tri-axial stress system.

Rotationally symmetric stress distribution Components of hoop stress
